US engineers' effort to make hypersonic vehicles faster, more affordable gets funding boost
- ritambhara516
- Apr 10
- 4 min read
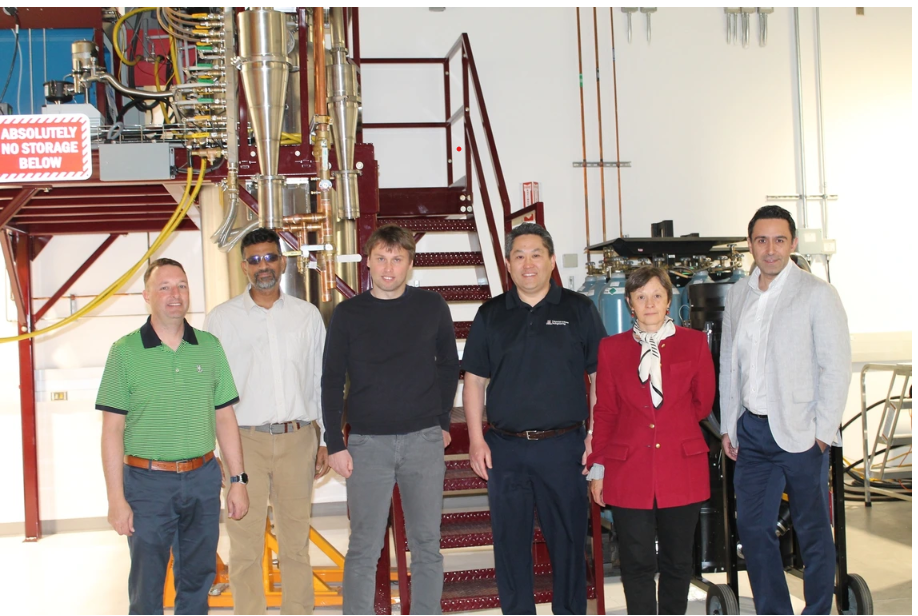
The Mach-X research team (from left, Andrew Wessman, Krishna Muralidharan, Benoit Revil-Baudard, Sammy Tin, Oana Cazacu and Kavan Hazeli) is working for the first time in the university’s Applied Research Building. The ARB offers a gas atomization system that produces metallic powders for 3D printing, among other equipment.
A University of Arizona engineering initiative aimed at making hypersonic vehicles faster and more cost-effective has received a $3.1 million grant from the U.S. Army. The funding supports a research team led by Sammy Tin, who holds the Patrick R. Taylor Endowed Department Leadership Chair in the Department of Materials Science and Engineering.
Tin and five fellow engineers from the university's College of Engineering are researching the use of advanced metallic alloys and additive manufacturing to help develop Mach-X—pronounced “mock-ex”—aerospace technology. These vehicles are designed to operate at speeds exceeding Mach 5, the threshold for hypersonic travel and five times the speed of sound. The project is part of a broader federal effort focused on advancing hypersonic technologies.
"This critical research collaboration leverages the university's strong foundation and targeted investments in hypersonics,” said Tomás Díaz de la Rubia, U of A’s senior vice president for research and innovation. “It also aligns with a core strategic objective of the university: strengthening leadership in space sciences, space technology, and national defense.”
The two-year research project will also contribute to wider national goals and help bring Mach-X technologies closer to real-world Army deployment, said David W. Hahn, the Craig M. Berge Dean of the College of Engineering. Additionally, the project will provide hands-on training for both undergraduate and graduate students, preparing them to fill essential roles in advanced manufacturing across the U.S.
Hahn added that the grant enables the college to fully harness its technical expertise and infrastructure.
“I expect this work will enhance the nation’s capabilities in homeland defense, space missions, and high-tech manufacturing,” he said.
An end-to-end environment
Sammy Tin and Andrew Wessman, an assistant professor in materials science and engineering, have collaborated on several hypersonics-related projects and collectively hold more than a dozen patents in alloy innovation. However, this is their first time working together in the university’s Applied Research Building, which opened in April 2023 to support cutting-edge work in advanced manufacturing and space science.
“The Applied Research Building allows us to handle every phase of the research process in one location,” said Wessman. “It enables us to work efficiently and build a complete understanding of which materials are most effective, which methods are successful, and what outcomes we can achieve.”
The research group also includes faculty members Krishna Muralidharan, Oana Cazacu, and Benoit Revil-Baudard from the Department of Materials Science and Engineering, along with Kavan Hazeli from the Department of Aerospace and Mechanical Engineering. They will examine two different alloys to assess how well they can be formed into the intricate shapes required for high-speed aircraft.
These alloys will be fused using 3D printing and a technique called compositional grading, which involves gradually transitioning the composition from one alloy on the exterior to another beneath. This design enhances the materials' ability to endure extreme temperatures and stress, dissipate heat efficiently, and prevent concentrated hot spots.
Tin’s team also plans to use an advanced powder atomizer and several metal 3D printers housed within the Applied Research Building to create new alloy materials from metallic powders. A specialized lab is being built within the facility to test how these materials perform under temperatures as high as 2,200 degrees Fahrenheit.
Aligned with national priorities
Over the course of the two-year grant, undergraduate students, graduate research assistants, and postdoctoral researchers will support faculty in tasks such as materials testing, modeling, and simulation. According to Wessman, this hands-on experience equips students with highly sought-after skills that are valuable to both government agencies and private industry. Gaining expertise in cutting-edge materials and production techniques will also prepare them to lead efforts in expanding the U.S. manufacturing sector.
“Having graduates who understand and can apply this knowledge benefits the nation across a variety of industries,” Wessman explained. “Beyond defense, they can contribute to sectors like automotive or consumer electronics.”
The research team also anticipates broader national benefits from the project. A key objective is to build a comprehensive understanding of 3D printing techniques, including the costs and trade-offs involved with different materials and processes. This knowledge will help advance the technology, enabling manufacturers to produce uniquely shaped components that are both cost-effective and feasible.
“One of the biggest hurdles right now is the lack of a manufacturing supply chain, which drives up the cost of hypersonic systems,” Tin noted.
Partnering in the project is the National Center for Defense Manufacturing and Machining (NCDMM), a nonprofit that connects defense stakeholders to accelerate technology development and integration. For this project, NCDMM will provide expert advice on aligning the research with user needs and help share findings with others working in national defense and innovation.
Tin believes that the materials and manufacturing methods developed through this research will eventually benefit space exploration and commercial aviation as well.
“Aircraft structures tend to share similar geometric designs,” he said. “This technology has the potential to impact many commercial sectors and significantly influence modern life.”
댓글